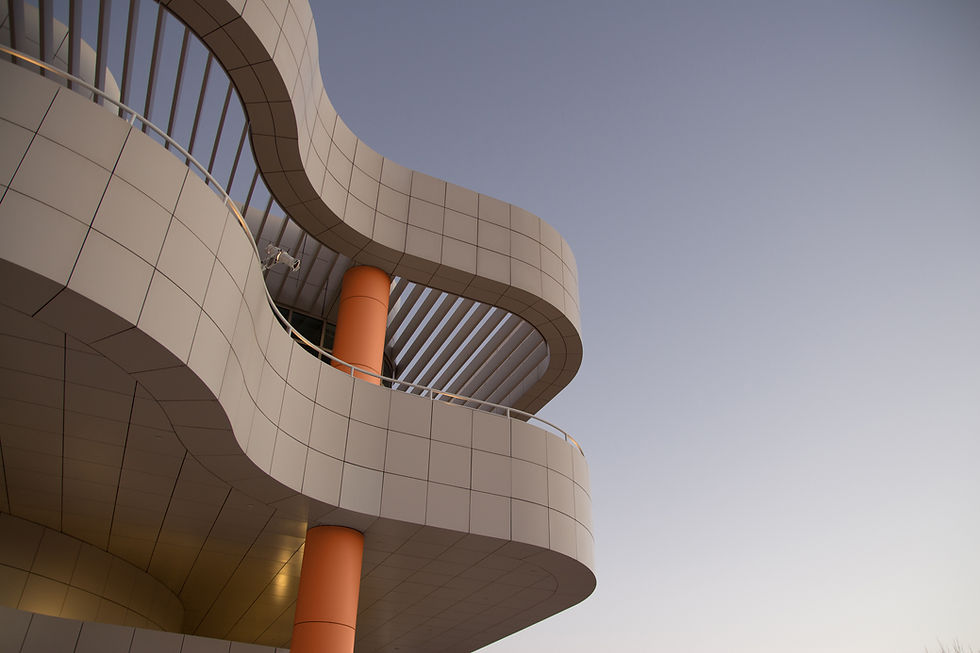
Revolutionizing Flexible Manufacturing Systems: A Step-by-Step Guide to Optimal Design

In the advancing world of manufacturing, the need for flexible systems that can adapt to changing demands and complexities is more crucial than ever. The diagram above provides an insightful look into the step-by-step design process for Flexible Manufacturing Systems (FMS), highlighting the importance of aligning production objectives with specific design criteria. Let's break down this FMS design journey to understand how expert tools, simulations, and advanced AI-driven analyses shape the best FMS outcomes.
Understanding Design Objectives in FMS
The foundation of any successful FMS design lies in clearly defined objectives. This initial phase sets the stage by considering production output, investment, resource utilization, and process time. Defining these parameters is essential for aligning the system with both current demands and future scalability. Once objectives are established, the design process can tap into the power of an expert system tool (AI-1) to initiate the FMS design. This AI-driven approach lays the groundwork for a more intelligent, adaptable, and efficient FMS.
Selecting Key FMS Components
The next phase involves selecting critical components that contribute to a robust FMS. Each element—machine tools, layout, transportation, storage design, inspection facilities, computing systems, economic considerations, and social aspects—plays a role in achieving a seamless, high-functioning system. By fine-tuning each component, designers can create an environment that optimizes performance and prepares for any operational challenges that might arise.
The Role of FMS Simulation Models
After assembling the components, the design process turns to FMS simulation models. These simulations test whether the design meets the predefined objectives. If the design does not satisfy the requirements, the simulation model allows designers to loop back and make necessary adjustments. This iterative process ensures that only the best possible configuration moves forward. When the objectives are met, the design advances to the next level, where tools like AHP (Analytic Hierarchy Process) help choose the best model, and performance measures are assigned weights to evaluate efficiency.
Integrating Advanced AI Tools for Optimal FMS Design
With the design objectives achieved, it’s time to leverage advanced tools to refine the FMS. Neural networks (AI-3) can be employed to weigh performance measures accurately, capturing the nuances of each component’s contribution to the overall system. Meanwhile, fuzzy set tools (AI-2) are used to define membership functions, providing flexibility and precision when setting design parameters. These tools make FMS design more adaptable, empowering the system to respond to changes and maintain efficiency under varying conditions.
Conclusion
The flexible manufacturing system design process is a complex yet rewarding journey. By aligning design objectives with simulation testing and employing advanced AI tools, engineers can craft a system that’s both resilient and efficient. This holistic approach enables FMS to adapt seamlessly to changing production demands, ensuring sustainable growth and operational excellence.