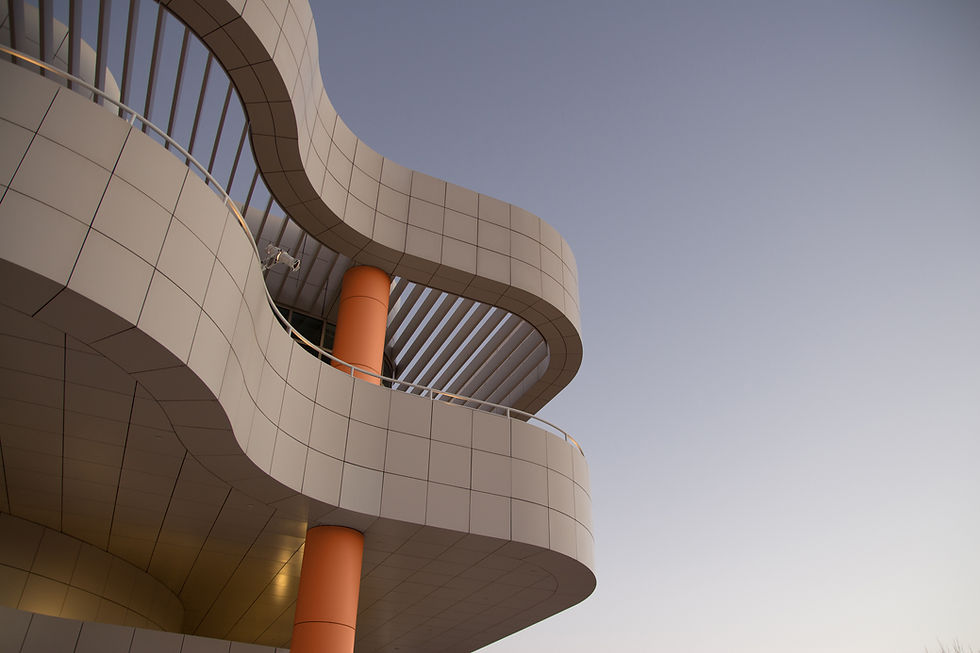
The Evolution and Future of Manufacturing Systems: From Initial Needs to Ramp-Up

In today's fast-evolving industrial landscape, the development and reconfiguration of manufacturing systems are more critical than ever. The need to stay agile and adaptive pushes companies to constantly refine their operations, optimize production, and embrace new technologies like digital twins and virtual simulations. This intricate process, shown in the diagram of manufacturing systems, provides a roadmap from initial needs to ramp-up and operation. Below, we’ll dive into each phase and how it impacts the entire manufacturing lifecycle.
A Comprehensive Look at the Future of Manufacturing Systems
The journey of a manufacturing system starts with defining Initial Needs. These are the foundational requirements, often identified in response to new market demands or internal operational goals. From here, companies can create a Design Plan tailored to meet these requirements.
Digital Transformation in the Manufacturing Space
As the manufacturing world leans towards digitalization, the inclusion of Digital Simulation, Virtual Production, and Digital Twins becomes essential. These technologies allow companies to create virtual models of their systems, reducing the need for physical prototypes and speeding up design adjustments. With digital twins, companies can simulate real-world performance, making reconfiguration, recycling, and retirement more efficient.
Building, Reconfiguring, and Recycling: The Practical Stages of Manufacturing
Once the design phase is complete, the Build/Construct phase kicks in. Here, the plans turn into physical infrastructure, ready to support production. But as market demands evolve, the need to Reconfigure becomes inevitable. This stage may involve adding, removing, or rearranging components, ensuring the system remains flexible and capable of adapting to new demands without starting from scratch.
The final stages include Recycle/Retire, where outdated equipment is either recycled or retired, and Ramp-up/Operate, marking the full deployment of the system to meet production goals. The reuse of components during the build and reconfiguration phases is also emphasized, aligning with sustainability goals and cost-effectiveness.
Conclusion
The future of manufacturing systems is bright, but it’s also complex and ever-evolving. With the right tools and strategies, companies can stay ahead by creating systems that not only meet current needs but are also ready for tomorrow's challenges. The use of digital simulations, digital twins, and a continuous feedback loop makes it possible for manufacturers to be resilient, sustainable, and highly efficient. Embracing these technologies and methodologies is no longer optional but essential for success in the modern industrial age.