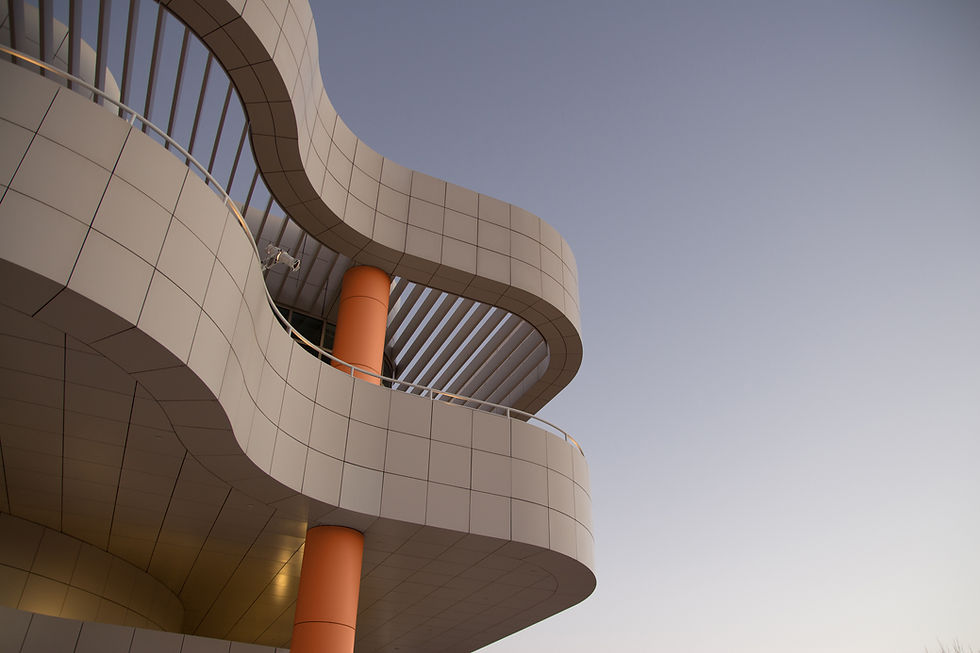
Understanding the Manufacturing and Assembly System: From Raw Materials to Quality Control

The modern manufacturing and assembly system is a complex process that transforms raw materials into finished products through a series of carefully managed stages. The diagram above provides a detailed representation of this system, illustrating each phase from processing and assembly to inspection and quality control. By understanding the roles of each element and flow within this system, manufacturers can optimize productivity and reduce waste, ensuring high-quality output.
Key Elements in the Manufacturing Process
The manufacturing and assembly system in the diagram comprises multiple elements, each contributing to the overall production flow. Here’s a breakdown of the primary components:
Process Stage: Represented by blue rectangles, these stages are the core operations where raw materials undergo transformation. Each process stage may involve various activities, such as cutting, shaping, and initial assembly.
Assembly Stage: Assembly stages are critical for bringing components together into a cohesive unit. During these stages, parts are combined according to specifications to create subassemblies or final products.
Inspection Stage: Quality checks are essential at various points in the manufacturing system. Inspection stages, depicted as pink squares, ensure that each part or product meets predefined standards. This stage identifies defective parts early in the process, preventing them from moving further along the production line.
Quality Controller: The diamond shapes represent quality controllers who oversee the inspection stages. Their role is to detect issues promptly and direct products needing rework or repair, maintaining high standards.
Queue/Buffer: Buffers, shown as yellow circles, serve as temporary holding points between stages. They balance the flow by managing congestion and allowing stages to process parts without delays.
Repair Crew: The green cross represents the repair crew, who manage defective products flagged during inspection. This team is responsible for addressing issues identified by quality controllers, ensuring minimal waste and efficient rework.
Production Control: Production control, symbolized by the blue oval, coordinates the overall manufacturing process, ensuring a smooth flow and addressing any disruptions.
Flows in the Manufacturing and Assembly System
Various flows in this manufacturing system illustrate how information and parts move between stages, allowing for a streamlined process:
Part Flow (Solid Black Lines): This flow represents the primary movement of parts through the production line. Each part moves sequentially from raw materials to processing, assembly, inspection, and, finally, quality assessment.
Information Flow: Out of Control Alarms (Red Dashed Lines): Red dashed lines signal alarms triggered by quality control points when a part or process deviates from set standards. These alerts enable immediate action, ensuring issues are resolved before they impact subsequent stages.
Repairmen Flow (Green Dashed Lines): When defects are detected, repair flows guide parts to the repair crew. This rework loop ensures that defective products are addressed without affecting the main production line.
Information Flow: Quality Correlation (Blue Dashed Lines): Blue dashed lines illustrate the flow of quality-related information between quality controllers and production stages. This continuous feedback loop is crucial for maintaining consistent product quality.
Ensuring Product Quality: The Role of Rework and Defect Management
The system emphasizes Rework for defective products. Parts or products that fail inspection are redirected to the repair crew for correction. This practice minimizes waste and boosts productivity by preventing defective products from reaching the final customer.
Conclusion: The Importance of a Structured Manufacturing System
This manufacturing and assembly system illustrates the importance of each stage and flow in achieving high-quality production outcomes. By integrating inspection, quality control, and rework processes, manufacturers can maintain efficient operations, reduce defects, and deliver products that meet the highest standards. Understanding and optimizing this system is key to achieving competitive advantage in today’s manufacturing landscape.